Our manufacturing in Bangladesh
In Bangladesh, our placemats and baskets are made from seaweed and jute. The products are made by hand using a sewing machine or just needle and scissors. The women and men who work in the factory are enormously skilled with the sewing machine and a placemat or basket can be produced in just a few minutes. Careful quality control of each product is usually carried out by women with long experience in the craft.
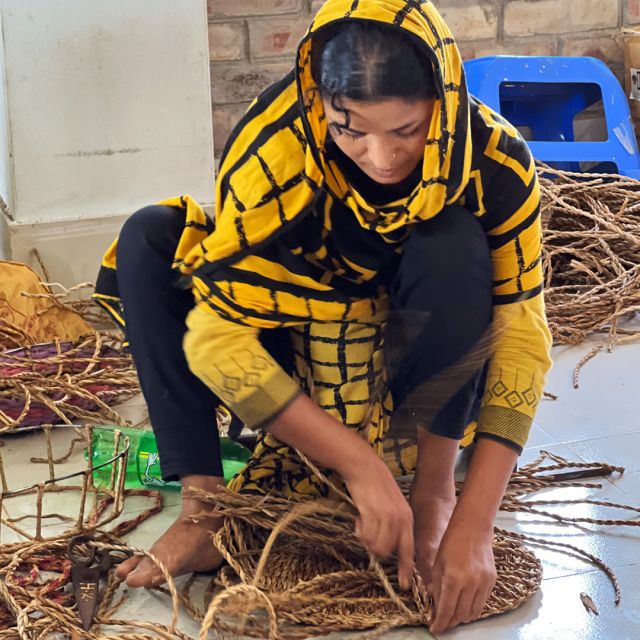
Coarse seaweed placemats are braided by hand using a needle and scissors.
Our manufacture of rugs in India
Almost all of our rugs are manufactured in India, both jute and rubber doormats as well as sisal rugs. All of our unique jute rugs are hand woven from machine or hand spun jute yarn. Our durable sisal rugs are machine woven on large automated factory looms.

A jute rug grows on a traditional handloom in Kerala -India
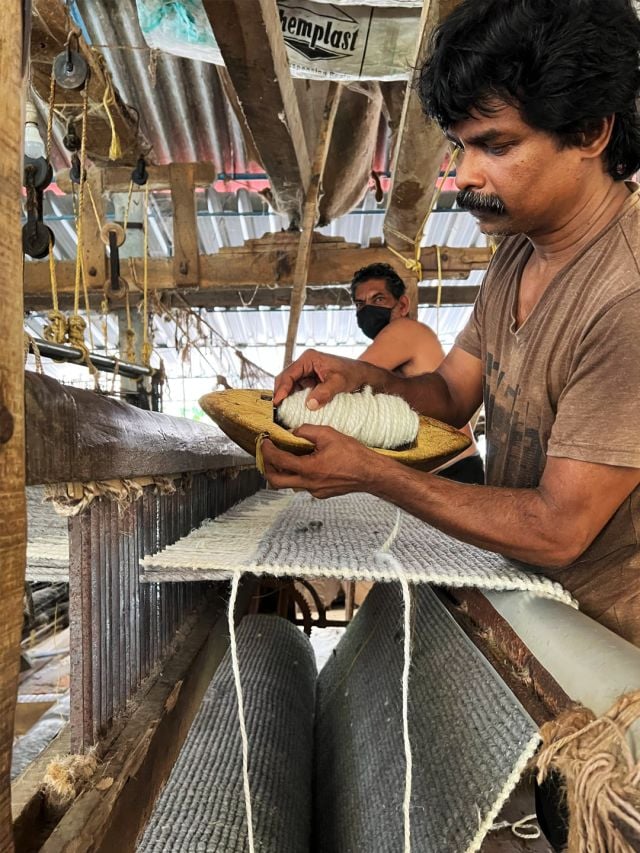
Shuttle is filled with jute twine
Waterhyacinth from Vietnam – Baskets that bind two worlds together
Many of our finest and most popular baskets are made by hand from water hyacinths in Vietnam. Water hyacinths are beautiful purple colour when they bloom. They cause a lot of problems though. They spread uncontrollably and clog up the watercourses that are an important source of fresh water around the Mekong Delta. The stalks can however be used. They are harvested, dried and hand woven by skilled craftspeople to become much-loved baskets and pouffes.
We are really proud of our baskets. Because of their attractive design, but perhaps most of all because of our long-term, close partnership with our producer in Vietnam. A well-run, sustainable factory a short distance from Saigon which makes the supply-chain of raw material both simple and cost efficient.
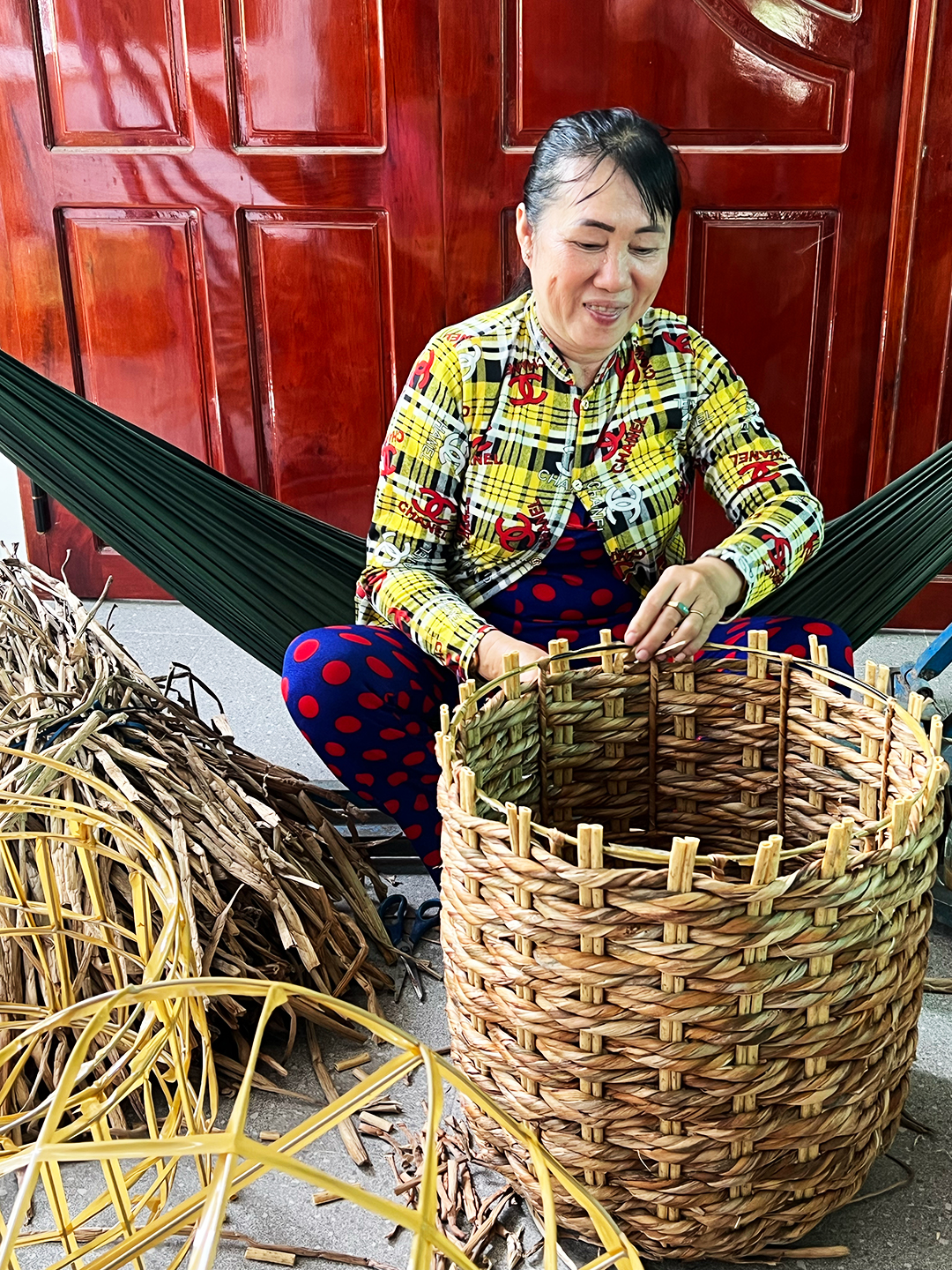
Weaving at home
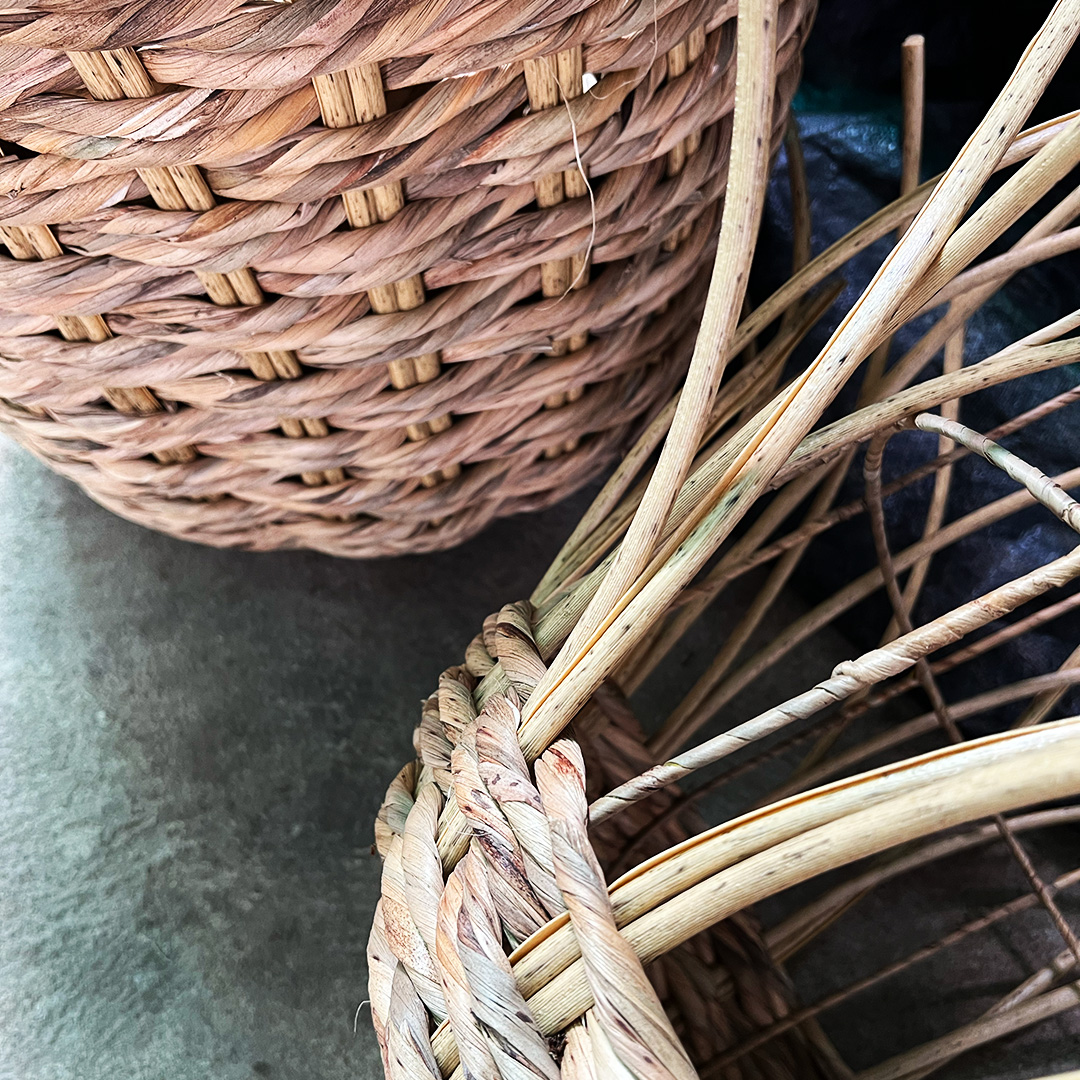
Baskets woven by hand
Natural, local production
We are really proud of our baskets. Partly for the good design, but perhaps mostly for our long-term and close collaboration with our manufacturers in Vietnam.
Our largest supplier has a well-run and sustainable factory located right on the river a few miles outside of Saigon. The location of the factory is very advantageous because the water hyacinth can be quickly and easily transported there after harvesting. In the case of full-scale production, the material is sent out to different families who weave, alternatively to a supervisor who also has the opportunity to store larger quantities of the material. She then distributes the work to other families in the village. The family, mainly the women, can then adjust their working hours based on everyday matters, such as the children’s school times and market visits.
Some farmers in the area both grow, harvest, store and weave the water hyacinth. Our supplier buys all the material they need from the farmers. They pay for the material per kilo and the weaving is paid per product. The price is set based on how much material is used. A twisted product is thus more expensive than a plain woven product. Not because it is more difficult to manufacture, but because more material is used when twisting the stems.
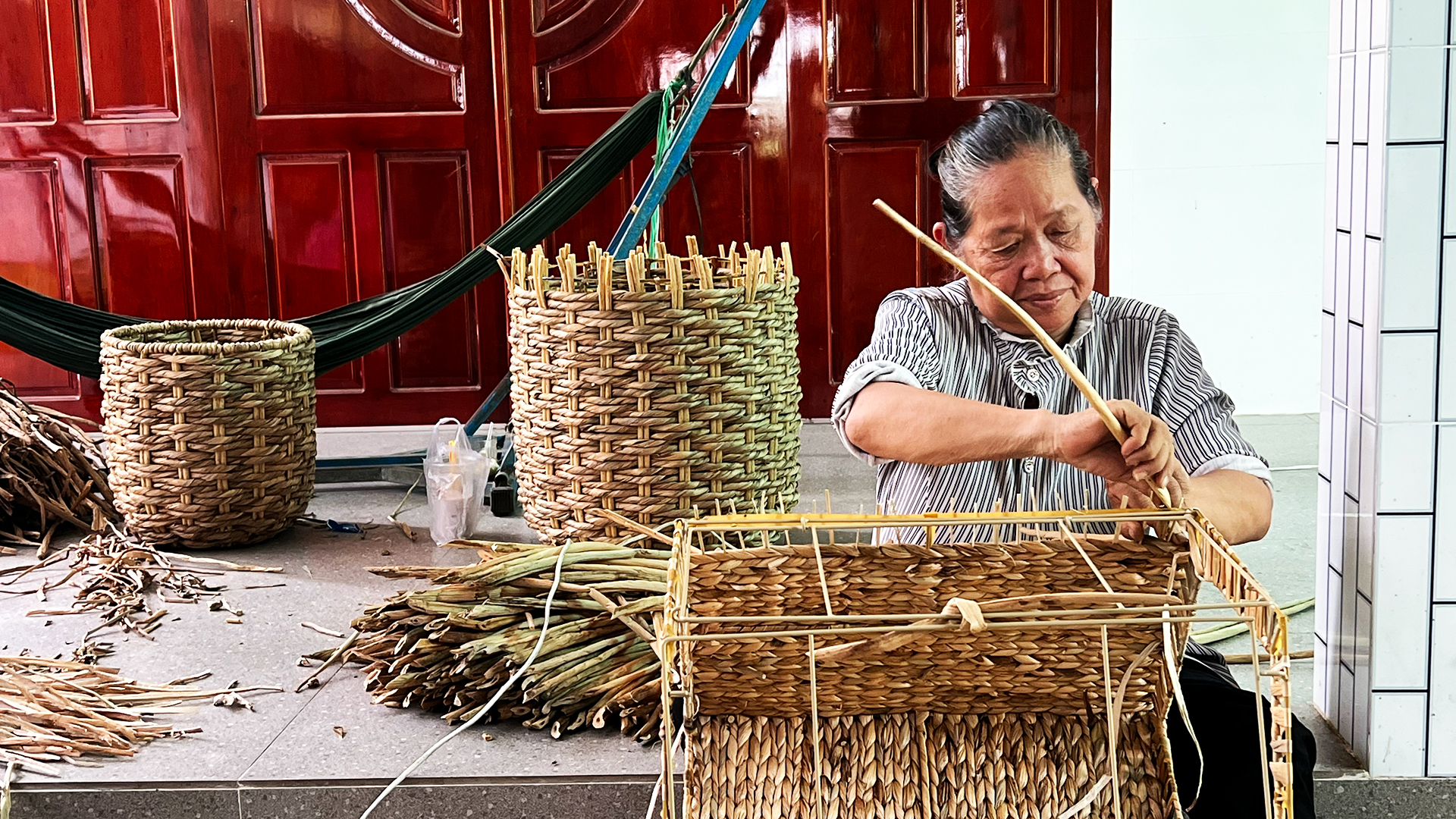
Weaving at home
A skilled craftsmanship of high quality
A handwoven product of water hyacinth is a fascinating work of art that is painted before our eyes. The craftsmen are extremely skilled and a beautiful basket emerges in just a couple of hours. The finished woven baskets are picked up and driven to the factory for finishing and quality control. The baskets are first rinsed clean with water and sprayed with environmentally certified starch that holds the fibers together. They are then dried in the sun or in large drying cabinets depending on the weather.
Finally, the baskets are stored in a warehouse with optimal humidity (30-60%) before they are packed and shipped by boat to us in Sweden.
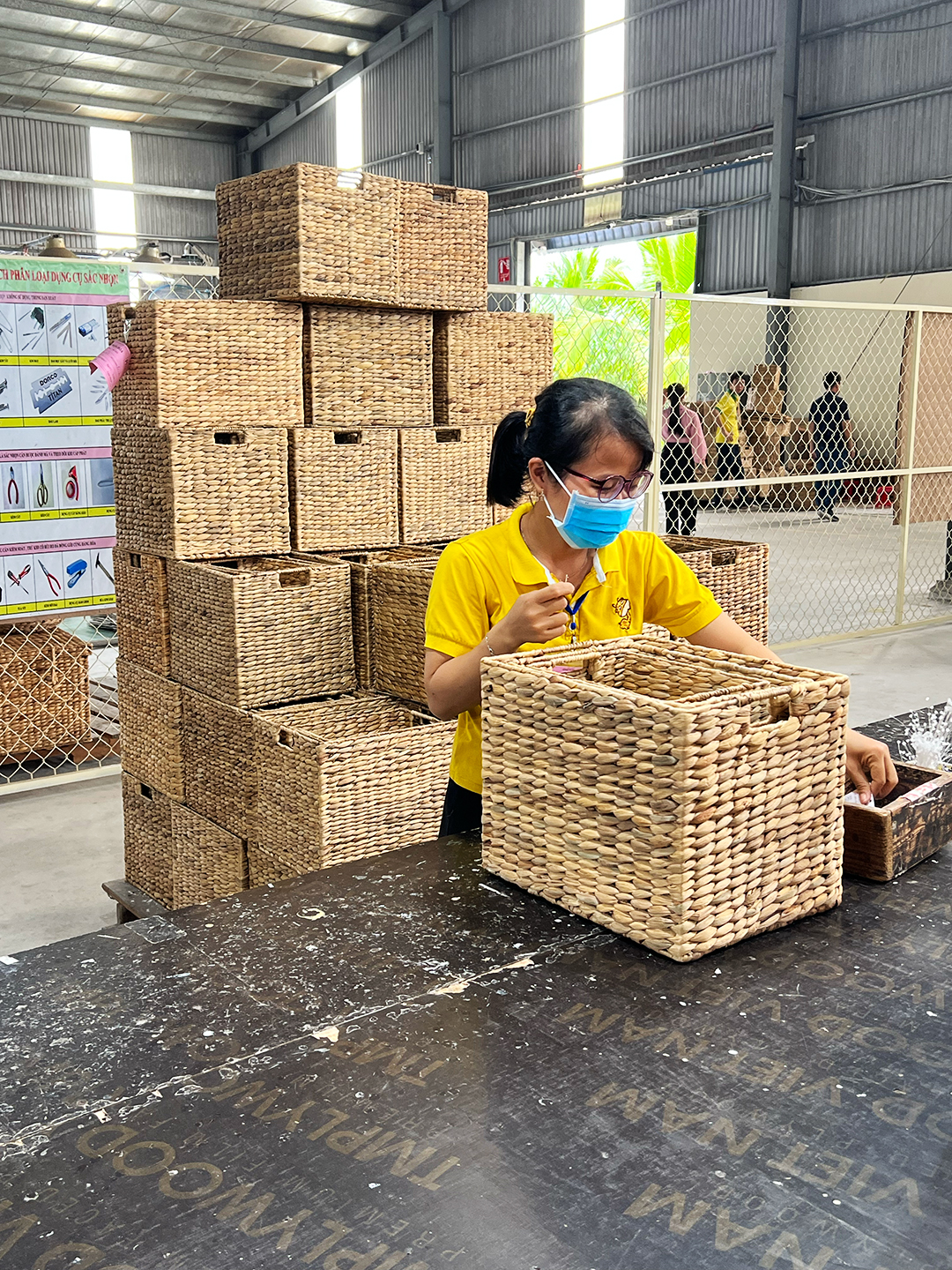
Quality control
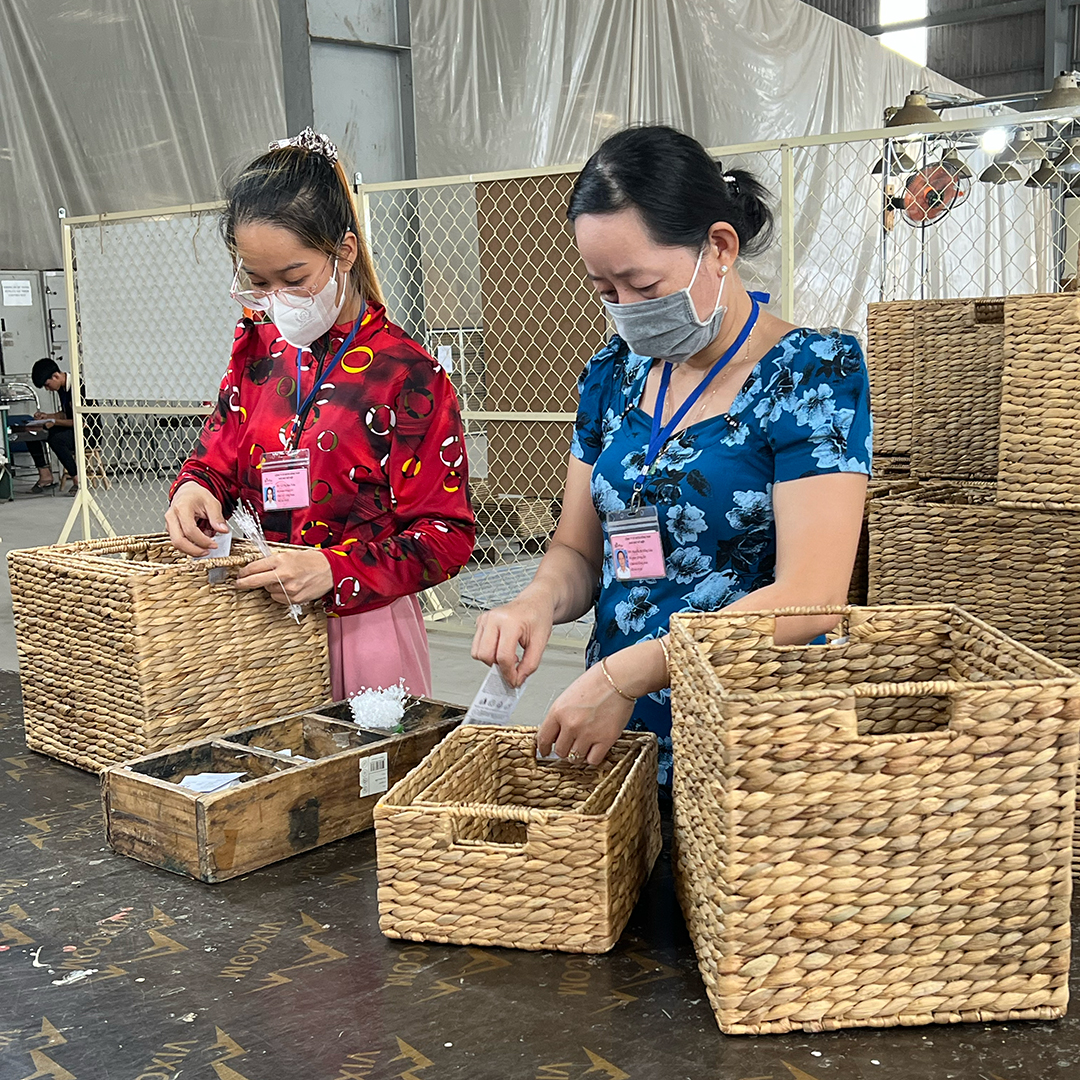
Quality control and marking
Quality control
All baskets are checked manually to ensure quality before packing and delivery. Material that sticks out is cut away and repaired and supplemented with new material if necessary. The basket then moves on to the next station, which is marking and checking the goods against a reference sample. There are clear instructions at every stage of the process. The quality controls are numbered so they know who has checked what, which makes the process traceable in the event of any inaccuracies.